The Power of Six Sigma Summary
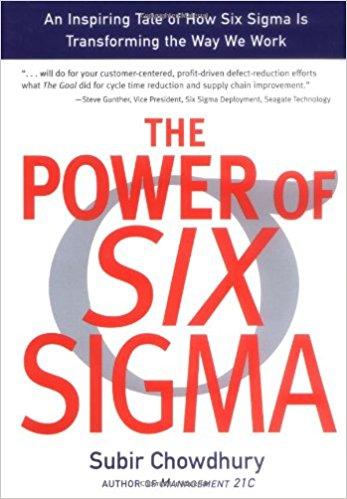
5 min read ⌚
An Inspiring Tale of How Six Sigma is Transforming the Way We Work
Have you heard about Six Sigma?
If you have, you already know its power. If you have not, it is time we introduce you to it.
Who Should Read “The Power of Six Sigma”? and Why?
Now before we tell you what “The Power of Six Sigma” is about, let us tell you what this book is not: it is not a guideline on the steps of implementing Six Sigma. It is also not written with the intention of the authors advertising themselves to you.
Then what is it?
It is a theoretical introduction to Six Sigma, and how it is continually transforming the business world.
It is a truly insightful book, which will unveil to you that the notion that Six Sigma has a hidden practical meaning which only some people know is untrue.
We recommend “The Power of Six Sigma” to anyone who has been or is becoming involved with this quality enhancement strategy.
About Subir Chowdhury
Subir Chowdhury is an author, which has received many awards for his leadership in quality management. He is currently executive VP of the American Supplier Institute.
“The Power of Six Sigma Summary”
Many companies started adopting Six Sigma over the past few years, although they did so without fully understanding the commitment it required.
As a result, many of them were disappointed at the end, not getting what they were expecting. But that outcome came as no surprise since companies were not acquainted enough with the practice, although they assumed they had enough insight to make Six Sigma work for them.
Instead, they followed Six Sigma success stories such as General Electric and Allied Signal and assumed it would automatically make their businesses thrive as well.
So far we have talked about the wrong ways of adopting Six Sigma, but we still haven’t explained its concept. We will cover that next: what is Six Sigma and what makes it so powerful?
Simply put Six Sigma is a system that combines process and people power.
In an ideal world, a company’s pool of employees will consist of productive and competent workers and brilliant researchers.
These researchers are not only focused on inventing intellectual capital, but they are trying to avoid costly errors as well.
In other words, with Six Sigma, money saved is money earned. Quality control is constant, and anyone can contribute to it.
So, whenever a company enters a Six Sigma project, it begins a task which needs to create more efficient operations.
If you are the one heading the project, then you should focus on saving as much money as you can, and the company will surely reward you.
In other words, your company will thank you for making its operations less costly.
But Six Sigma is not a one time project. It is a management philosophy which allows the people who implement it to measure the exact impact of the changes they brought in the usual processes.
Although Six Sigma is a philosophy that, once comprehended, guarantees success, many employees and companies are hesitant to try it out, since during their careers they have seen many initiatives designed to improve operations fail.
However, even the greatest skeptics cannot negate the power of Six Sigma once they adopt it.
Of course, the impact of Six Sigma will vary depending on each process the company performs. But, that is completely normal, since no company ever succeeded producing a product with 100% consistency.
Now, during your life, you may have accepted the misconception that there is always a trade off between lower costs and better quality, and that may be keeping you back from adopting quality enhancement strategies.
If you are in such a mental place, it is time to change your mindset – you will not benefit from it.
Go even a step further and teach your employees that improving quality and reducing costs is not only possible but needed.
Another thing Six Sigma will do for you, except saving you money, is increasing the customer satisfaction levels. Your employees (especially your accountants) will be happier too since fewer warranty reimbursements and discards will mean that the tug of war between the employees and the customers will no longer exist.
If we managed to convince you that you can solve your problems with Six Sigma, we need to warn you not to try to address all your issues at once.
Instead of trying to figure out what works and what doesn’t, listen to the market. Your customers and their experiences will show you where you need to improve.
We understand that you may want to fix everything at once, but believe us; it will work against you.
So, stop multitasking and focus on one project at a time, until you are completely satisfied with the outcome.
Key Lessons from “The Power of Six Sigma”:
1. Where Should You Start?
2. Defining Roles
3. Start at The Beginning
Where Should You Start?
When starting out, pick the most easily solvable item.
When you solve this problem, you will present the value of the program, easily create savings and increase customer satisfaction.
Then you will have a greater motivation to move forward.
Defining Roles
It is important for Six Sigma for your employees to know their roles. But, although a project needs a leader and employees that support the leader it is not just another top-down initiative.
However, each project needs to have someone who will maintain the direction until the very end.
Some of the roles are:
-
- Project champions
-
- Black belts
- Green belts
Start at The Beginning
When you start Six Sigma, do two things: define the issues you face and set a numerical goal.
Do not focus on the final problem – focus on the process that causes it. And remember, Six Sigma’s goal is not only improving quality but also saving money and increasing customer satisfaction.
Like this summary? We’d Like to invite you to download our free 12 min app, for more amazing summaries and audiobooks.
“The Power of Six Sigma” Quotes
The main thrust of Six Sigma is to reduce errors and waste in every kind of business endeavor to please customers and fatten the bottom line. Share on X Sigma is like a measurement, used to determine how good or bad the performance of a process is; in other words, how many mistakes a company makes, doing whatever it does. Share on X Six Sigma companies learned that quality saves money because there are fewer throw-outs, fewer warranty payouts, and fewer refunds. And doing all that, in turn, increases profits. Share on X Never tell people how to do things. Tell them what you want to be done, and they will surprise you with their ingenuity in getting there. Share on X Pick the problem that’s giving you the most trouble, the one that’s costing the company the most, the one that’s making customers unhappy. That’s the one that will reward you the most if you can fix it. Share on XOur Critical Review
“The Power of Six Sigma” is an excellent outline of the theory behind Six Sigma, and is a recommended read for all people who want to get introduced to this method and its principles.